For most maintenance crew members, cleaning equipment is one of the last jobs of the day. There’s a good chance their minds have already wandered to after-work activities and family. Although it’s an area that is often overlooked, proper equipment cleaning practices can prevent many time consuming and costly repairs down the road.
“Equipment managers should really look at daily cleaning as part of preventative maintenance,” said Greg Walker, Technical Training Manager for Jacobsen. “By spending just a few minutes at the end of each day properly cleaning equipment, operators can actually save their facility money.”
The most common failures on a machine can almost always be traced back to water intrusion: relays, switches, coils, bearings, bushings. Some of this comes from normal operation in the rain, dew, etc, but many issues are the direct result of water and debris intrusion from cleaning. It’s typically not one improper cleaning session that causes issues, it’s usually a series of repeated events over time.
The two most common mistakes made when cleaning equipment is using too much water and using too much pressure. Excess water or pressure can force contaminants such as dirt, grass, and top-dressing sand into the bearings and bushings thus causing premature wear on metal-to-metal contacts like lift arms and rollers.
Areas where grease has been washed away must be re-greased immediately to prevent wear and rust.
Serious damage can occur if water also makes its way into electrical parts like the instrument panel, relays and switches. This can cause serious damage – especially if it’s reclaimed water, which can be very corrosive.
Other serious problems can arise if machines are cleaned when still hot. Spraying hot electrical coils with cold water shortens their life. Make sure all equipment has properly cooled before cleaning and never wash a running machine – water intrusion into the engine can cause it to seize up.
To help prevent water and debris intrusion when cleaning equipment, experts suggest using a ¾” hose or smaller and keep the PSI under 60. However, the best solution is to use compressed air. For facilities that don’t have air, backpack blowers work great. Ideally, you should use water on the rotary blades and reels and compressed air on everything else. Using a pressure washer is never recommended.
Rich Stuns is the Equipment Technician at Washington National Golf Club, a beautiful course outside of Seattle. Several pieces on Stuns’ fleet are actually more than twelve years old and have over 7,000 hours on them.
“We take good care of the equipment here,” said Rich. “I think the guys take better care of it when it looks good. I will even wax the hoods as a final touch. I’ve found that my Jacobsen equipment will last forever if maintained properly. We make it harder for neighboring courses to get new equipment because they think everyone should get 12 years out of a mower.”
By implementing some common-sense cleaning procedures, you can save time, money and headaches over the long run.
Author: Adam Slick is the Public Relations & Communications Manager for Jacobsen. Slick has a Bachelor of Arts degree from St. John Fisher College (Rochester, NY) and is currently working on his MBA at Colorado State University. Contact Adam at [email protected] or 704.504.4867.
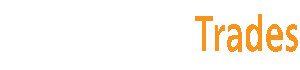